Dairy Shed Showering System
- IM Dairies
- Jun 2, 2017
- 7 min read
In Pakistan, summers can be harsh on humans as well as cows. Temperatures usually run as high as 45-50 degree Celsius. Hot winds further exaggerate the heat impact. In some areas humidity coupled with high temperatures can be fatal to exotic breed cows. While local breeds have evolved over centuries and can easily tolerate the hot summers, the exotic breeds are intolerant to this scorching heat. Therefore, farmers who keep exotic breeds, must adopt measures to mitigate the impact of excessive heat.
Temperature alone is not the only factor that causes heat stress to the cows. Heat stress is caused by a combination of temperature, relative humidity, solar radiation, air movement and precipitation. The majority of studies on heat stress in livestock focus on the two main environmental stressors: Temperature and relative humidity (RH)1.
The relationship between temperature and humidity and the subsequent heat stress is depicted as “Thermal Heat Index” (THI). The chart below shows the heat index and the stress that cow feels when subjected to a specific heat index:
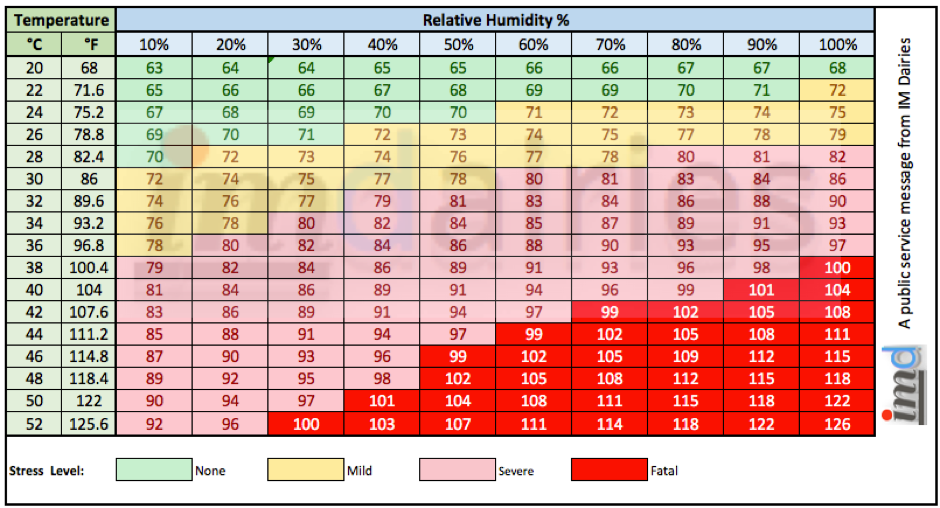
In the area where IM Dairies is located (70 Km from Multan, Pakistan), the temperature during June can be as high as 50 Degrees Celsius. Thankfully, the area has low humidity all year around. The humidity in June usually remains below 10%. As per the above chart the THI in June can go as high as 90, which puts our cows in Severe Heat Stress. If we don’t take corrective measures the cow’s wellbeing will be severely impacted.
One of the most effective measures against heat stress is the installation of shower and fans. Please note that the prescription presented in this article is specific to our farm’s situation (high temperatures and low humidity). You should fully understand our rationale of this prescription and then take adequate measures for your farm. Blindly following what we prescribe here without fully understanding the rationale behind it – may cause problems at your farm.
The current capacity of our farm is 100 adult animals. We are building it in two phases and in the first phase we have completed the shed for 50 cows (25 on the right and 25 on the left). The shed dimensions are shown in the diagram below:

To install the showering system, here is what you need:
Water Pump, Pipes & Showering Nozzles:
We have installed 2HP (1.5 KVA) water pump. The underground drinkable water level in our area is around 20 feet. So, we have drilled a 20 feet bore and our 2HP pump is sufficient to meet not only all our showering needs but also all other water needs (e.g. filling water tanks, cleaning the farm etc.). Given below is the schematic diagram of how the pipes have been laid in our farm.

Following points should be considered while installing the pump and the pipes:
The 2 HP pump that we use at our farm, pumps water out from a depth of 20 feet and then pumps the water into the pipes with a total length of approximately 160 feet. If you are pumping water from a water tank as opposed to extracting it from the ground then your 2HP pump can run pipes with far greater length. Even with our setup the pressure that we get with a 2HP pump is far more than the minimum required for showers to operate properly. We believe we can probably run pipes with a length of 400 feet or more with our existing 2HP pump. We did consider installing 1HP pump; but given our future plans of extending our shed we thought it best to install 2HP pump, even though it is probably more than our current needs.
The nozzles should be installed at a minimum height of 7’ from the floor i.e. 7' above the cows hoofs while in standing position.
The shower nozzles should be placed at a distance of 5' from each other. This is because our nozzle’s spray diameter is around 5’. If you want to be absolutely accurate with the nozzle distance then simple test your nozzle’s spray diameter. If it is less that 5 feet then you should reduce the distance between the nozzles if it is greater than 5 feet; then you can either increase the nozzle distance or stick with 5’. Having a smaller than required distance between the nozzles is not harmful it only increases the water volume that is showered onto an animal. Since our feeding deck is approximately 55 feet long therefore we have installed 12 shower nozzles on each side of our shed, for a total of 24 shower nozzles.
We have used 2” diameter pipes all around.
If you have to run the pipe to greater lengths then do note that the water pressure will decrease in proportion to the distance from the pump. Therefore, you would probably need to cross over your 2” diameter pipe to a smaller diameter (e.g. 1.5” or even 1”) for the last 15-20% of the pipe segment.
If your pump gets its water from a water tank (as opposed to pumping it out of the ground); do make sure the water temperature does not exceed 33 C. In summer, the water in the water tanks can easily go as high as 45 C. Your cows will probably not stand under the showers if the water temperature is that high.
We have installed shower nozzles that are specifically made for dairy farms. We purchased them from Bilal Switchgear Engineering, Lahore. Each shower nozzle costs Rs. 450. We have seen people using Pesticide Spray nozzles instead – which are very cheap and can also serve the purpose. We recommend using the pesticide spray nozzles first. If you are not happy with the results then you can replace them with the ones from Bilal Engineering.
In the video below we have shown the showering nozzles that we use at our farm (purchased from Bilal Engineering):
Fan:
Both shower and fans go hand-in-hand. One without the other will not have the desired effect. Therefore, in addition to the shower, you also need to install fans. Fans facilitate evaporation – which cools the cows down. I have seen farms which obsess about showers but do not switch on the fans as often as they should or their fans are not properly installed.
At IM Dairies we have installed industrial strength 1.5 KVA (2 HP) single-phase fans. These fans have a throw of 15 feet x 50 feet. This means that our fans can circulate air in an area of 15’ x 50 ‘. If you look at our shed diagram – this fan is ideally suited for us since our shed length is 55’. We have installed one fan on each side of the shed. We have purchased our fans from Bilal Switchgear Engineering, and each fan costs Rs. 29000. Given below is a photo of the fans that we have installed at our farm.
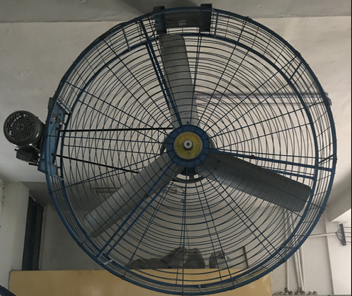
Most of the farms that we have seen use simple ceiling fans. We had the following considerations in choosing which fan to install:
A ceiling fan rotates the existing air in the area. This limits its effectiveness. We wanted the air to circulate in a tunnel profile as shown in the diagram below. Due to the tunnel profile the fan does not circulate existing air instead it moves along the fresh air.
We would have needed 20+ ceiling fans to cool the cows as opposed to the two 1.5KVA fans that we opted for.
Typical ceiling fan consumes 100-120 watts and costs between Rs. 3100- 4000. Therefore, ceiling fans would have cost us in access of Rs. 60K and would have consumed 2000-2400 watts. The two industrial dairy fans cost us 58K and consumes 3000 watts. Based on these considerations we concluded that the price and electricity consumption comparisons put both the options at equal footing; and industrial fans are undoubtedly more effective. Therefore we decided that the industrial dairy fans would be more suitable for IM Dairies.

Please note that installing these industrial fans is difficult and can rarely be done by a local electrician. You would need specialist to install these fans. We do plan to write an article on fan installation as soon as we have some time to spare, In Sha Allah.
Timer Switch Board:
Thankfully the cows do not need the shower and the fans all day along. The need is usually critical between 12:30 pm – 4:00 pm. The shower and the fans need to be switched on in a synchronized manner. First the cows need to be showered and then the fans should be switched on – at no point in time should both the showers and the fans be on simultaneously.
Switching on the fans while the cows are being showered will result in spraying the water all over - thereby making the feed wet. To help wtich the shower and the fan on/off in a coordinated manner you would need a timer switch. You can get the switch made to order from Hall Road in Lahore and/or from other electronics markets in your city. The outlets that construct switch boards will ask you for your specifications and will then construct a switch board with the timer made to your specifications (see schematic diagram below).
We got our timer switch board developed from Bilal Switchgear Engineering. It cost us Rs. 40K. If we were to get it developed from Hall Road, Lahore it would probably have cost us half of this price. We spent more money because Bilal Switchgear Engineering only gives warranty of their fans if you run it with their timer switch board. Therefore, we didn’t want to take any risks and wanted to have peace of mind.

Please note that we did experiment a bit before we were able to get our showering system absolutely right. Don’t be afraid to experiment. Having said that, before you undertake the installation of the showering system – make sure you understand the design philosophy and rationale behind all the components of the showering system. Only then will your experiments bear fruits. For example, despite the lecture that we gave you about fans; we did not install our fans for several weeks. This is because in our farm high cross winds blow all day around and we were able to get along fine with just the showers. Similarly we did not install the timer switch for several weeks; we were happy switching on/off the showers manually. We first got the showers right and then we installed the fan and the timer switch.
Check out the video below; which was made during the initial days of our showering system – when we had only installed 25% of the showering system and the fans and timer switch hadn’t yet been installed.
References:
THI Calculation by Todd Bilb [http://www.progressivedairy.com/ ]
[https://imdairies.wixsite.com/home]
Sprinkler Systems for Cooling Dairy Cows at a Feed Line by Joseph P. Harner et. al, Kansas State University, USA.
Comments